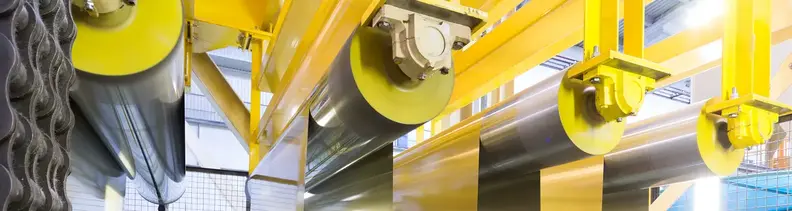
Aluminium Rolling Fluids
What are TotalEnergies' aluminium rolling fluids?
To produce aluminium plates and sheets that have high-quality edges, no defects including no staining and are uniform in thickness and width requires the use of durable yet precise metal working machinery
Due to the pressures and work involved with rolling aluminium, rolling mills and their constituent components need to be properly lubricated, a task that TotalEnergies' range of reliable aluminium rolling fluids easily fulfil, safeguarding equipment from wear and damage.
For optimum metal working, TotalEnergies' selection of lubricants used in aluminium rolling comprises:
- Lubrilam – Cold rolling oils and additive concentrates
- Vulsol MSF 5200 – Roll grinding oil for cylinder grinding
- Osyris – Roll protection oil for corrosion prevention
- Vaona MQL – Edge trimming oil
- Martol EV/LVG – Fast-vanishing tension levelling and stamping oils.
- Martol FMO – For food packaging.
- Martol AL – Aluminium stamping and wire drawing oil.
- Azolla AL – Non-staining hydraulic oil for rolling mills.
- Carter – Non-staining gear oils for working and back-up rolls.
Why choose TotalEnergies' aluminium rolling fluids?
TotalEnergies' wide selection of aluminium rolling fluids have been designed and formulated to provide lubrication across several steps along the aluminium rolling production line, ensuring that parts are able to safely and effectively perform without undergoing undue metal wear or corrosion.
Geared towards the needs of aluminium rolling operations, they also have low volatilities, quick-drying properties and high flash points among many other features and benefits, delivering clear efficiency gains and cost savings. Part of the Total Metalworking lubricant range.
TotalEnergies' aluminium rolling fluids’ key features and benefits
The TotalEnergies aluminium rolling fluid range have been formulated with help from industry to provide the following features and benefits:
- Multipurpose oils – For simple and efficient lubrication
- Excellent cooling properties – Extending lubricant change intervals and the lifetimes of products
- Extreme pressure resistance – To protect tools from corrosion and metal wear
- Exceptional anti-wear properties – Reducing component change frequencies
- Low volatility – For a safe lubricant that evaporates quickly
- Biodegradable – To safeguard food and the overall environment
- Detergent additives – For less downtime spent cleaning
- Transparent appearance – For better conditions when machining
- Oxidisation resistance – Lengthening the lives of lubricants and tools
- Low or no odour – For a more pleasant working environment
- Quick drying action – To minimise downtime
- Very good adhesiveness – To aluminium surfaces
- High flash point – Limiting the risk of fire in the facility
- Less carbonaceous matter and residues – Reducing cleaning frequency
For more information on TotalEnergies aluminium rolling lubricants or to make an order, please contact our team.